Everything you need to know about Digital Twins
Posted 6 Jul 2022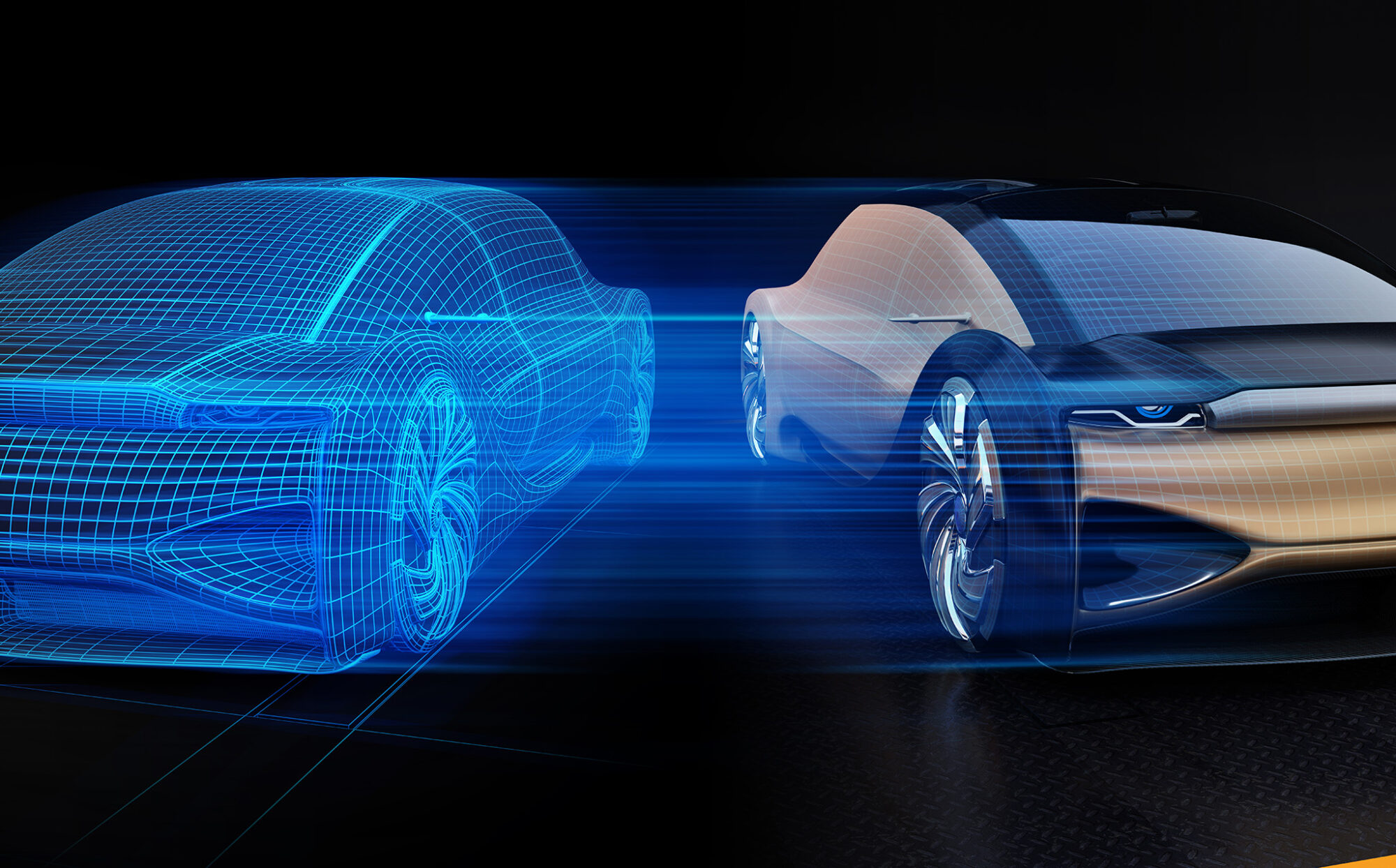
Everything you need to know about Digital Twins
Imagine you are the owner of a manufacturing company and one of your most important pieces of machinery breaks down. What do you do? Your first port of call would usually be to find a specialist nearby who may be able to fix it. You book an available time slot with them. They travel to your premises, take apart the machine, and diagnose the problem.
But what if, instead, you could establish the problem quickly and remotely, without the need for someone to travel to your site or dismantle your machinery? Or what if you had been able to predict that your machine might fail and had replaced the necessary parts ahead of time? These are just a few examples of how digital twins will soon transform how many industries operate.
What are Digital Twins?
Put simply, a digital twin is a virtual representation of a real-world asset or process. This could be anything from a piece of software to a machine, a building, or federated digital twins addressing an entire industrial supply chain.
From an oilfield or a construction site, to a network of buildings or even an entire city, the value of advanced cyber physical systems is gaining recognition across the board. The same digital twin technologies used in many industrial applications have also been used by doctors to create digital versions of human organs, they’ve been used by forestry management companies to model forests, and they’ve been used to create omniverses that simulate physical processes. They can be applied to many situations, and combined to address many issues.
Digital twins share the same qualities as existing tools like digital models, but they take this technology one step further, taking information and updates from its real counterpart using sensors and other IoT and 5G devices and connectivity. Using AI/ML and simulation, the digital twin can be used to remotely monitor processes and productivity, identifying improvements and malfunctions, carrying out ‘what if’ analyses, predicting events and suggesting solutions.
The twin is essentially a living and breathing pre- and post-production model that evolves along with the physical asset for the entire duration of its lifetime. Tests and simulations or even training, however, can be carried out on the digital counterpart without affecting the item or system in the real-world.
How are Digital Twins useful?
One of the most obvious benefits of using digital twins is their efficiency in predictive maintenance. The process of maintaining and repairing an asset is enhanced significantly, automating the prediction of when parts will fail and the diagnostics and for unknown issues remote access and visualisation allowing it to be analysed in real time by the best qualified person anywhere in the world. And quicker diagnostics means less downtime.
Even the likelihood of malfunction is minimised. With a digitised version available for testing, simulations can be conducted at any time, enabling engineers to effectively predict and prevent problems before they have a chance to arise.
The digital twin can gather information integrating IoT sensors, visualisation and high performance networks. The virtual model can analyse this information to monitor ‘wear and tear’ and simulate deterioration on an ongoing basis, without the need for periodic visual inspections, which can have large margins of error.
This combination of monitoring and simulation is particularly useful for large assets, such as bridges, buildings. These entities can be tested through simulations throughout their life-cycle: at the design phase, during construction to map against design ambitions, and then during operation – to ensure everything is working optimally.
Taking action on supply crises
With supply chains in disarray and resiliency measures rendered uncertain, many businesses have struggled to adapt to shifts in global supply networks. Changes to supply chain processes are fraught with risk, with companies often unwilling or unable to take the chance and move to a new model.
Digital twins can use data simulations to gather information and test the robustness of supply chains during the digital modelling phase – prior to their implementation. Adjustments made at this stage can significantly reduce risks by allowing companies to predict and solve issues early on, saving them time, money, and their reputation further down the line. This can be extended in life with digital models connected across organisational boundaries to optimise and adjust the supply chains as the supply and demand shifts in different places.
The future of Digital Twins
Digital twin technology is still very much in its nascence, but it is growing in momentum, especially in the UK. In fact, digital twins were ranked highly in our Digital Future Global Index, while nearly half (48%) of UK manufacturing leaders said they would be investing in Digital Twins at some point in 2022. Meanwhile, the projected global market size of digital twins is expected to hit £48.2 billion.
Building on the successful implementation of standalone digital twins is the idea of interconnecting them, which has huge potential when it comes to addressing systemic problems, such as sustainability. Therefore, interoperability is vital, along with digital security, trust, and openness.
More than being ‘a technology’, connected digital twins are a means of integrating technologies to achieve a defined purpose – making better decisions faster.
“It’s this integration of technologies in the service of ‘information flow’ that holds the promise: from the use of sensor technology, 5G and IoT to get data from the physical world into digital twins…to immersive visualisation tools such as AR/VR/MR to facilitate human/digital twin interaction.
Mark Enzer, OBE CTO of Mott MacDonald and Head of the National Digital Twin Programme at the Centre for Digital Built Britain
Arguably, Digital Twins involve a collection of different technologies, including IoT, data collection, storage and analysis, network connectivity, simulation, AI, and the growing use of immersive technologies. In order for them to reach their full potential, connectivity is key, with fast and reliable digital infrastructures necessary for facilitating live digital coupling. Thankfully, the UK is second in Europe in terms of its 5G infrastructure rollout, and we see this underpinning connectivity as instrumental in bringing in the next stage of digital twins’ technological development.
Now, Digital Catapult is working with Connected Places Catapult on its Digital Twin Hub – a community bringing together industry and academia to explore the use of digital twins across industry and help shape the future of the built environment in the UK. Hub membership currently stands at more than 3,500 individuals, representing more than 1,600 organisations from nearly 80 countries.
While challenges of interoperability, security and connectivity remain, with our strong performance in many technology areas, and impressive levels of investment, the UK has the critical building blocks in place for taking digital twin technology to the next level.
To learn more about the future of advanced digital technologies, including more information on digital twins, download our Digital Future report.
Digital Catapult newsletter
Receive articles and insights like this delivered directly to your inbox
Subscribe now